Key technical facts
In short
Spartan Robotics was in the process of selecting a cobot manufacturer to best position them to develop a cobot welding cell that could serve the market to its fullest. The 7th axis of the Kassow Robots cobots provided a unique differentiator and a reliable component for their system, leading to the decision to select a cobot that could provide greater flexibility for welding cell design. Spartan Robotics required a cobot that could handle complex welds, integrate smoothly into the Spartan Welder, and offer reliability for end users. The Kassow Robots' 7th axis and robust construction proved essential in creating a system capable of precision welding, reduced maintenance, and efficient deployment. The integration of Kassow Robots enabled the Spartan Welder to achieve precision welding in hard-to-reach places, significantly improving weld cycle times and overall workflow efficiency. Kassow Robots' use of premium components, such as metal internal components, provided enhanced reliability and minimized maintenance concerns. This strategic decision allowed Spartan Robotics to create a highly dependable cobot welding cell, positioning the company to expand its offerings and deliver increased productivity and consistent quality to end users.
.jpeg)
Challenge
Spartan Robotics, a division of BlueBay Automation, needed to select an optimal cobot manufacturer that addressed specific requirements for robotic welding applications. Traditional robotic systems, such as industrial robots and other 6-axis collaborative robots, proved inadequate for performing complex welds in confined spaces. Specifically, 6-axis cobots often struggle with obstacle avoidance in cluttered environments, which is critical when welding in tight areas. Additionally, maintaining consistent torch tip speed during complex weld paths is a challenge for 6-axis models, leading to inconsistent weld quality.
The additional axis provided by Kassow Robots helps to overcome these limitations by allowing smoother, more controlled movements, ensuring precision even in difficult welding scenarios. This highlighted the need for a more adaptable and collaborative solution with greater maneuverability and precision. Spartan Robotics aimed to select a cobot that could be seamlessly integrated into their welding cell, providing end users with enhanced production efficiency, improved welding precision, and reduced downtime.
By selecting Kassow Robots, Spartan Robotics ensured that the end users of the cobot welding cells would benefit from faster deployment, minimal programming requirements, and a system capable of handling complex welds where other cobot brands fall short.
Solution
Spartan Robotics chose Kassow Robots for their distinctive 7-axis design, compact footprint, and extended reach, which provided end users of the cobot welding cells with greater flexibility in where they could deploy the system. Whether positioned in tight facility corners or confined spaces, the Kassow Robots cobots enabled more versatile placement options, making them well-suited for welding in challenging environments. The flexibility of Kassow Robot’s cobots allowed end users of the Spartan welding cell to leverage a single cobot for multiple welding applications, significantly reducing setup time and increasing overall productivity. This flexibility also meant that end users could adapt the system to a variety of welding tasks without extensive reconfiguration, providing them with a versatile solution capable of handling diverse production needs efficiently.
Leveraging the available API, the company developed a customized CBun (Capability Bundle) plugin, incorporating tailored welding functions including linear, arc/circular, stitch, and touch sensing to name a few, that streamlined the user-friendly interface. In addition to these welding functions, Spartan Robotics also developed CBuns for servo-controlled positioners and automatic tool changers, which further enhanced and expanded the system's capabilities. These additional CBuns allowed seamless integration of positioners for optimal part orientation during welding and automatic tool changing capabilities, making the system even more versatile for diverse welding tasks. This initiative simplified cobot management by providing intuitive welding-specific controls, which reduced the learning curve for operators. Rapid operator training was facilitated through pre-configured welding sequences and easy-to-use interfaces, allowing users to quickly master essential welding tasks. Additionally, this significantly improved workflow efficiency for end users by minimizing downtime and ensuring consistent weld quality, even in complex welding environments.
Benefits
The integration of Kassow Robots provided significant advantages for Spartan Robotics and, most importantly, for the end users of the Spartan Welder. These benefits include:
- Heightened Welding Precision: The 7-axis design allowed for better maneuverability, enabling precise welds even in difficult-to-reach areas, which is crucial for quality outcomes in complex welding scenarios.
- Reduced Cycle Times: The advanced flexibility of Kassow Robots reduced the need for constant repositioning, which in turn shortened weld cycle times, allowing manufacturers to improve overall throughput.
- Improved Workflow Efficiency: Kassow Robots' user-friendly interface and integration capabilities made it easier for operators to get up to speed quickly, minimizing training times and reducing programming complexity. This allowed manufacturers to optimize production schedules and keep operations running smoothly.
- Reliability and Reduced Maintenance: Kassow Robots' use of metal gearing enhanced the overall reliability of the welding cell. This reduced maintenance frequency and minimized unexpected downtime, ensuring that manufacturers could depend on the Spartan Welder for consistent production quality.
By standardizing their welding cell with Kassow Robot’s cobots, Spartan Robotics positioned itself to deliver customized, efficient solutions that directly benefit end users. Kassow Robots' association with Bosch Rexroth further bolstered confidence in the product’s reliability and performance, leveraging Bosch Rexroth's esteemed reputation for engineering excellence to enhance the brand's credibility.
This strong foundation has positioned Spartan Robotics to expand its automated welding solutions with more advanced features, including enhanced weld path control, increased adaptability for diverse manufacturing setups, and more specialized welding capabilities. These advancements aim to boost efficiency, drive higher productivity, and directly address the specific needs of customers seeking reliable and high-performing welding automation solutions.
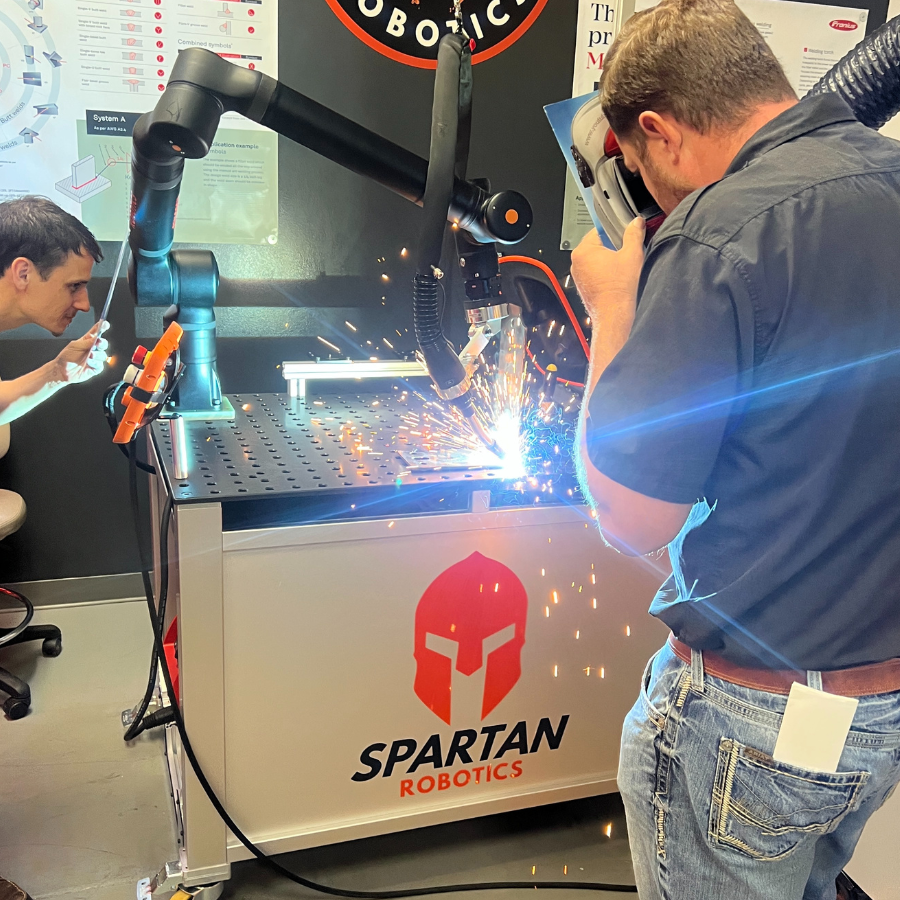
Our technology in use.
Easy-to-integrate solutions for a wide range of applications and industries.
A global partner network.
Become a part of our mission.