Key technical facts
Interview with Dr. Christopher Petry, founder of Tenta Vision GmbH in Trier, Germany
Multi-award-winning start-up Tenta Vision from Trier approached the PTS Group – a sales partner of Kassow Robots in Germany – with the following brief. “We want a robot that enables our inspection system to move over items with as many degrees of freedom as possible.” The result was a systems solution using the Tenta Vision Inspection System, a 7-axis cobot from Kassow Robots, and various components supplied by Bosch Rexroth. This patented product development is based on the doctoral thesis written by Dr. Christopher Petry, Tenta Vision’s founder. We spoke with Dr. Petry and asked him about his innovation, why he decided to use robots, andwhat convinced him that Kassow Robots was his best choice.
Dr. Petry, how would you describe your innovation to a friend who is interested inknowing more, but who is not an expert in technical matters?
Our Tenta Vision Inspection System uses a laser to look inside components made from all manner of lightweight materials, allowing it to precisely analyze their mechanical propertiers in real time and identify even minuscule defects. The heart is our compact measurement instrument, its brain is special automation software, and the cobot from Kassow Robots is a reliable assistant.
I would also like to say something about its areas of application. The building blocks for this system originated in the aerospace sector. What we have done is to automate this technology and make it significantly more robust, so that it is capable of withstanding its first-ever deployment in the demanding conditions of industrial production. We see ourselves as game-changers as a result, including for the automotive industry. Here, for example, we have presented the world’s first non-destructive bonding inspection. In addition to the automotive industry, we believe that our solution has a particularly brightfuture in electronics encapsulation and fiber-reinforced lightweight components.
Why did you decide to use a robot here?
We are able to identify defects that cannot be seen from the outside, but which would result in the component’s failure if they are not found. After all, we are dealing with very precise and comprehensive inspections of weak spots in a wide range of materials at extremely small scales – we’re talking nanometers. Our technology satisfies the pressing need for extremely high-quality automated inspections in this area. Kassow Robots’ cobots are extremely innovative, and that makes them ideal for innovators like us when we are looking to demonstrate that technology can be automated quickly and accessibly for everyone. This type of inspection work is normally performed by developers. It is a task that requires a great deal of hard work, and companies have to invest a lot of time in it. We want these companies to know that they can entrust these painstaking tasks to our automated system – so that their developers have more time to devote to other tasks. It is an approach that saves companies money while also helping to increase employee loyalty tothe company. It allows developers to spend more time giving free rein to their creativity instead of being bogged down by monotonous tasks. With our solution, all a company has to do is push a button and the Kassow Robots cobot gets rightdown to work – 24/7 if need be. And if it is necessary, it can share the same workspace with employees – naturally this is checked for each individual application.
And if I could add a few words for those who would like to know about a bit more about our product ... Our technology analyzes the distortion of an object, for example of a plastic component. Using the energy we feed it, the camera records an object’s weak spots in real time. It is precisely these weak spots of an object that we are able to measure. Even deformations at a nanometer scale tell our customers that a component is defective.
Why is it that a Kassow Robots lightweight robot has been entrusted with moving themeasurement instrument to the precise locations needed, and not a different robot?
We actually conducted tests with various cobot manufacturers, and Kassow Robots’ cobot proved to be the best product. It was PTS Group, a systems integrator from Germany, that drew our attention to Kassow Robots, which is part of Bosch Rexroth. After this, things moved quickly, because we knew that they were the right choice. The fact that Kristian Kassow – a genuine cobot pioneer – is behind these 7-axis cobots is also a bonus.
As an engineer, it goes without saying that I expect extremely high levels of quality and precision, and I want to use only the very best technology for our customers. The following three criteria were particularly important for me: 1.) lightweight construction that is suitable for industrial use; 2.) the greatest possible flexibility; and 3.) simplicity of use. After all, we have to focus on what our industrial end customers are looking for. This means not just major corporations, but SMEs as well. That is because our solution also makes sense for these small and medium-sized operations. We want to reach customers who are new to robotics and make our solution as compact and user-friendly as possible.
You mentioned how important flexibility was to you – what is it that Kassow Robots’ cobot offers here?
When it comes to flexibility, it offers fivefold benefits for our solution – I would like to list all the features that were decisive in our selection of a robot manufacturer: 1.) Unlike conventional cobots, those produced by Kassow Robots do not have six axes, but rather seven – this 7th axis allows them to “see” around corners. They are also very mobile and compact. We have complex structures, and the camera has to be able to see into even the most hard-to-reach places. To do this, we need a cobot with the flexibility toexecute these movements. 2.) Thanks to the 7th axis, this solution can also be provided in compact form. And it can be used in extremely specialized areas of application. Space is always an issue – that is why we wanted to supply a compact system that can fit in anywhere. 3.) This cobot is very light: the smallest model weighs just 23.5 kilograms, meaning that it remains mobile, and 4.) there is a wide product range able to bear loads of up to 18 kilograms, with ranges of up to 1.80 meters, and finally 5.) KR cobots are really easy to program and operate.
What target groups are you reaching with your comprehensive solution featuring acobot?
As mentioned previously, our solution can be a real help for SMEs and major corporations alike. Take SMEs, for instance: these companies might first want to familiarize themselves with the technology and use this solution forspecific spot-check inspections. In addition, when we are talking about really large quantities that are being manufactured with short cycle times, our Tenta Vision System and its cobot can also be integrated into fully automated production processes. Here, our solution takes over the 100% inspection as part of quality assurance, for example end-of-line inspections.
Tenta Vision is a young company that believes in robots, but this is the first time you are using a robot in your own company. What do you recommend for those who are new to this field?
We also have a fundamental understanding of programming – even so, it is always a good idea for those who are using robotics in their companies for the first time to work with a systems integrator. For us, we continue to work with the PTS Group – they remain a valuable source of advice and serve as our ‘sparring partners,’ and they conceived the comprehensive solution. Not only did we acquire the Kassow Robots cobot from PTS, but also a mobile workbench that was specially developed for our application on which the cobot is mounted. PTS supplies the rugged supporting frame made of Rexroth aluminum profiles that was designed to allow it to fit through 90-cm doorways. PTS used a 3D printer to produce connecting parts made of high-quality Onyx filament material. The mobile workbench means that the solution can be easily transported from A to B–so it is not tied to any one location. It can simply be moved to wherever our system is really needed.
The PTS team did a great job, and we are thankful to have such honest and expert partners at our side. That’s why I can truly say that newcomers should investin a systems integrator when undertaking their first project in particular.This will increase their know-how and provide them with expert support whenever questions arise.
Is it true that you also liked the appearance of Kassow Robots’ products?
Yes, it is. The first time we were introduced to them, we thought that their black cobots were a great fit with our black inspection system. Obviously, this was not the deciding factor – that was the fivefold flexibility of Kassow Robots: this really is added value!
Thank you for your time, Dr. Petry!
© Kassow Robots
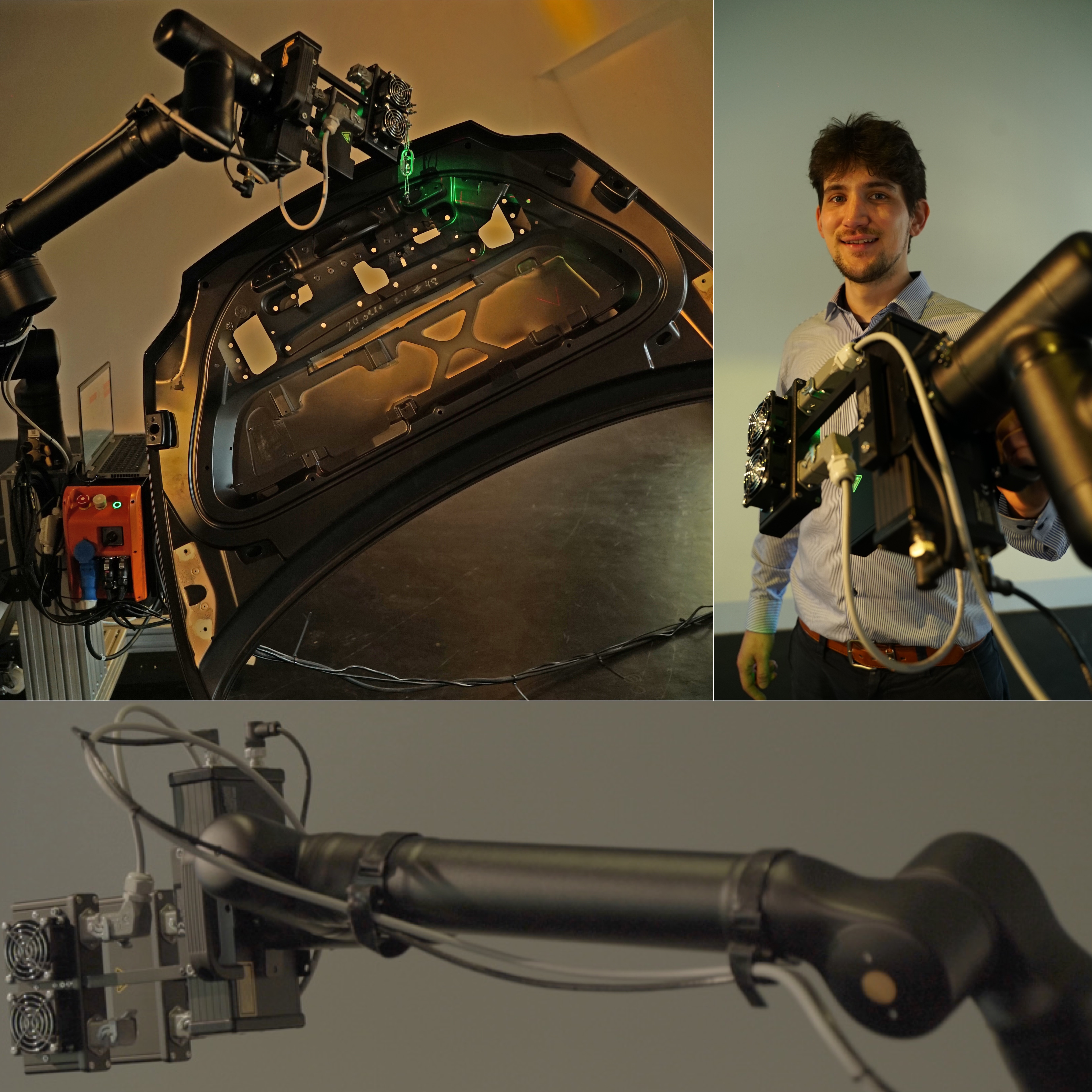
Our technology in use.
Easy-to-integrate solutions for a wide range of applications and industries.
A global partner network.
Become a part of our mission.