Facing challenges in logistics and warehouse management is a common hurdle for manufacturing and distribution companies.
One such challenge is understanding what a palletizer is and how it can impact efficiency for industries operating in different sectors.
Palletizers are automated systems designed to stack products onto pallets, which has reshaped the packaging and distribution process. They are capable of managing various product types and sizes and have become essential in today's logistics, helping to make operations more efficient and flexible.
This guide will look into the essentials of palletizers, paying close attention to their design, functionality, and their role in streamlining packaging operations. You'll learn how these machines not only expedite product handling and improve reliability but also promote safer work environments by minimizing manual labour.
What is a Palletizer and How it Works
A palletizer is a machine engineered to automate the process of stacking products onto pallets following a specific pattern. This automation is key to improving the packaging process by making it faster, more consistent, and safer.
The primary benefits of using a palletizer include increased efficiency through quicker packaging times, improved stability of the stacked products to minimize damage during transport, and a reduction in the physical strain on workers, which lowers the risk of injury.
Palletizers are versatile and capable of handling a wide array of product types, from boxes and bags to barrels and bundles. This adaptability makes them suitable for various industries, including food and beverage, pharmaceuticals, and manufacturing.
They work by receiving products on a conveyor belt, organizing them into the desired pattern, and then methodically stacking them on a pallet.
Advanced models can adjust to different pallet sizes and product dimensions, further optimizing the packaging line for different operational needs.
By streamlining the process of preparing goods for shipment, palletizers play a crucial role in logistics and supply chain management.
Their ability to automate stacking tasks boosts productivity and contributes to a smoother, more reliable flow of goods from manufacturers to consumers.
Types of Palletizers
Palletizers are primarily divided into two categories: conventional and robotic.
Conventional palletizers are known for their speed and efficiency in environments with uniform product sizes, utilizing mechanical means to stack goods.
Robotic palletizers offer greater flexibility and precision, employing advanced technology to handle a diverse range of product types and packaging configurations.
Each type presents distinct advantages that benefit different operational needs, from high-volume production lines to those requiring adaptable solutions for varied products.
Conventional Palletizer
Conventional palletizers make use of mechanical systems for operation and have been a staple in packaging lines for decades.
They work well in settings where products are uniform in size and the volume of goods to be palletized is high. These machines are designed for speed, efficiently organizing and stacking products to maximize throughput.
Floor Level Palletizers: Operating at ground level, these palletizers are easily integrated into existing packaging lines. Their design eliminates the need for structural changes to the facility, making them a cost-effective solution for many operations.
Floor level palletizers are accessible for maintenance and monitoring, making them a popular choice for various industries.
High-Level Palletizers: These palletizers function by stacking products from a height, which allows for quicker operation. The design of high-level palletizers enables them to handle a broader range of product sizes, offering flexibility in packaging operations.
Their elevated operation improves the efficiency of the stacking process, making them suitable for operations looking to boost productivity and accommodate diverse product dimensions.
Robotic Palletizer
Robotic palletizers present a great evolution in palletizing technology, offering unmatched flexibility and precision in handling different products and packaging configurations.
These systems make use of advanced robotics and intelligent software to adapt to various operational demands, making them ideal for industries with diverse product lines.
Cobots (Collaborative Robots): Cobots are a subset of robotic palletizers designed to safely work in close proximity to human operators.
They are particularly useful in environments where manual and automated processes need to integrate with each other.
Cobots are compact, easily programmable, and can be adjusted for different tasks, making them a versatile tool in the packaging process. Their design prioritizes safety and efficiency, allowing for a collaborative workspace where robots and humans can perform side by side.
Articulated Arm Robots: These robots are known for their flexibility and range of motion, capable of performing complex stacking patterns that require precise movements.
Articulated arm robots can handle products of different shapes and sizes, from small, delicate items to larger, bulkier goods. Their advanced design enables them to quickly adapt to different packaging needs, reducing downtime and increasing productivity.
This adaptability makes articulated arm robots a valuable asset in modern packaging lines, where demand and product specifications can change quickly.
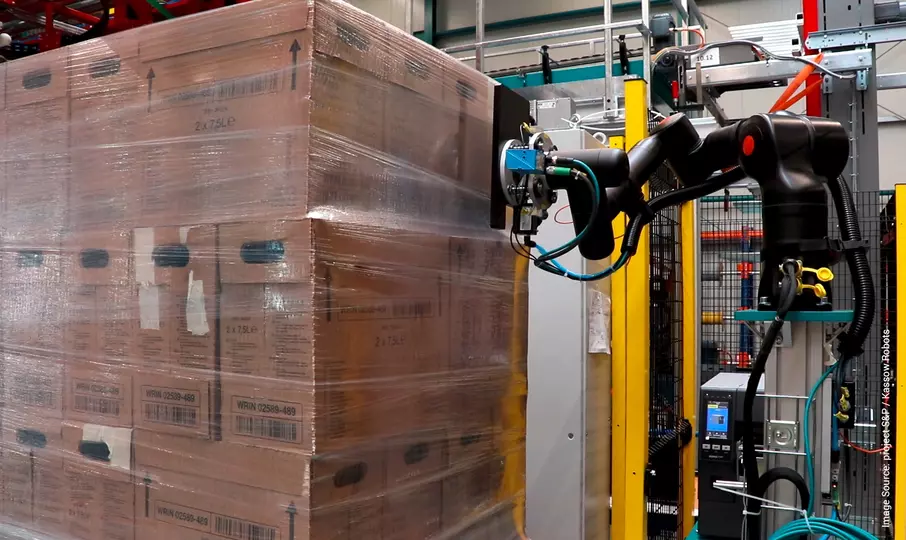
Robotic Palletizing Vs Conventional: Which is Best?
The decision to use robotic palletizers versus conventional palletizing systems depends on specific operational needs, including the nature of the products, the volume of production, and the amount of flexibility needed on the packaging line.
Kassow Robots offers a compelling solution with its 7-axis collaborative robot arm, which brings advanced versatility to robotic palletizing.
{{cta}}
This product is highly beneficial in environments that need adaptability and precision as they allow for more complex movements and the ability to handle a variety of tasks.
It is a great choice for businesses looking to enhance efficiency and adaptability on their packaging lines.
Let’s look at the differences:
Conventional Palletizers
- Food and Beverage Industry: Ideal for high-volume production lines where products like canned goods or bottles are uniform in size and shape.
- Manufacturing of Consumer Goods: Suitable for places producing large quantities of identical items, such as household products.
- Building Materials: Effective for stacking uniform items like bricks or tiles, where speed is crucial.
Robotic Palletizers
- E-commerce and Retail: Offers the ability to handle a wide variety of product types and sizes. Best for businesses with diverse inventories.
- Pharmaceuticals: Suitable for factories that need precise handling and flexibility due to changing package sizes and the delicate nature of products.
- Custom Packaging Operations: Great for businesses that need to quickly adapt to changing packaging needs or product designs. This allows for the ability to reprogram the robot for different tasks.
The History of Palletizers
Palletizers were first introduced in the late 1940s and completely changed the packaging industry by automating the process of stacking goods onto pallets.
Initially developed to enhance efficiency and safety in the food and beverage sector, these machines quickly became essential across various industries due to their ability to speed up the packaging process and reduce manual labour.
The advent of palletizers marked a huge leap forward in logistics and supply chain management, allowing for faster production lines, decreased risk of worker injury, and improved load stability during transport.
Over the years, technological advancements have led to the development of more sophisticated palletizing systems, including robotic palletizers, which offer greater flexibility and precision.
Today, palletizers are indispensable in sectors ranging from pharmaceuticals to construction, highlighting their critical role in modern manufacturing and distribution workflows.
What Are the Different Types of Pallets?
Pallets are essential tools in the logistics and supply chain industries, serving as the base for storing and transporting goods.
They come in various materials, each offering unique benefits suited to different needs. Understanding the types of pallets available can help businesses optimize their operations and choose the right pallet for their specific requirements.
- Wooden Pallets: The most common type, known for their strength and durability. They can support heavy loads and are easily repairable but may be susceptible to moisture and pests.
- Plastic Pallets: These pallets are lightweight, durable, and resistant to moisture, chemicals, and pests. Ideal for clean room environments, such as food and pharmaceutical industries, though they are more expensive than wooden pallets.
- Metal Pallets: Made from materials like steel or aluminium, metal pallets are extremely strong and durable, perfect for heavy or high-value loads. They are also fireproof and resistant to rot, but their high cost and weight limit their use.
- Paper Pallets: A sustainable and lightweight option, paper pallets are best for light loads and single-use applications. They are recyclable and have a lower environmental impact, but lack the durability and load-bearing capacity of other types. Paper pallets are useful in air freight due to their lightweight nature.
Palletizers FAQ
What is the Purpose of Palletizing?
The purpose of palletizing is to systematically arrange products on a pallet, ensuring they are securely stacked for efficient transportation and storage. This process improves the safety and organization of goods, resulting in smoother logistics operations.
Conclusion
Palletizers are key to boosting efficiency and safety in packaging and distribution.
While conventional palletizers are good in high-volume settings with uniform products, robotic palletizers do well with versatility and precision, ideal for handling a mix of products.
This makes robotic systems an ideal fit for sectors like e-commerce and pharmaceuticals, where product variety and packaging needs are always changing.
Kassow Robots' 7-axis collaborative robot arm stands out in the robotic space, as It combines flexibility with precision and is capable of complex movements to meet a variety of operational demands.
Whether you're looking to upgrade your packaging line or integrate more adaptable solutions, Kassow Robots offers the technology to enhance your efficiency and adaptability.
{{cta}}